The installation and commissioning of industrial plants for metals processing involves complex engineering works.
The installation stage involves erecting the major equipment and systems as per the engineering drawings and specifications. Equipment such as furnaces, reactors, smelters, conveyors, heat exchangers etc are installed along with the piping and ductwork systems. Electrical systems including cables, switchgear and motors are connected. Instrumentation and control systems are hooked up to sensors, valves and actuators.
Commissioning follows installation and includes functional testing of individual units as well as integrated system testing under simulated and actual process conditions. Trials are run to optimize the plant’s performance and ensure it meets design parameters and output specifications.
Industrial factories, steel, copper, aluminum
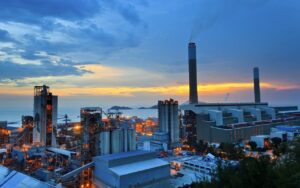
Once operational, planned maintenance and turnaround activities keep the plant running efficiently. Regular maintenance checks and overhauls of equipment are scheduled to minimize breakdowns. Turnarounds involve plant shutdowns for extensive maintenance and component replacement.
The engineering design of such industrial plants requires expertise in process engineering, mechanical engineering, electrical engineering, instrumentation and control engineering. The design has to account for thermal and flow characteristics of the metal processing, requirements for heating and cooling systems, material handling, pollution control systems, automation and safety features.
Proper installation, commissioning and maintenance backed by good engineering design ensures metals processing plants like copper smelters, aluminum refineries, iron and steel plants operate productively over many years with minimum downtime. Ongoing improvements and modifications also keep the plants optimized for changing market needs.